ตัวอย่างการประหยัดพลังงานจากระบบอากาศอัดในอุตสาหกรรมอาหาร (Case Study)
ตัวอย่างการประหยัดพลังงานจากระบบอากาศอัดในอุตสาหกรรมอาหาร (Case Study)
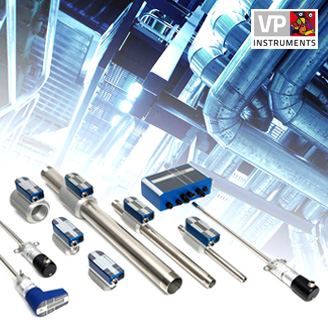
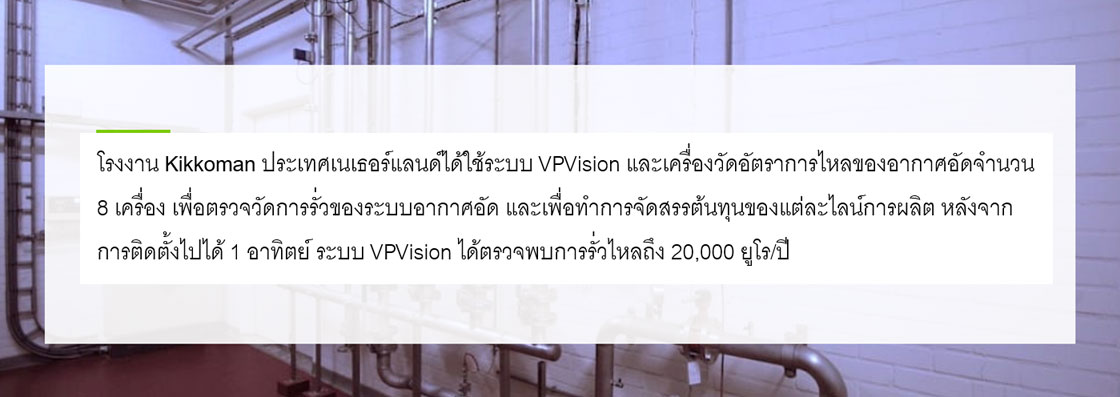
คณะกรรมการด้านการประหยัดพลังงานที่ Kikkoman
Kikkoman Foods Europe BV ได้ทำการผลิตซอสถั่วเหลืองญี่ปุ่นที่มีชื่อเสียงและเป็นที่รู้จักทั่วโลก เพื่อขายในตลาดยุโรป โดยโรงงานตั้งอยู่ที่ Hoogezand Sappemeer เมือง Groningen ประเทศเนเธอร์แลนด์ มาตั้งแต่ปี 1997 ซึ่งได้มีการผลิตซอสตามแบบฉบับที่สืบทอดกันมากว่าร้อยปี โดยเมื่อ 6 ปีที่แล้ว ได้มีการจัดตั้งคณะกรรมการด้านการประหยัดพลังงานขึ้นในโรงงาน โดยมีวัตถุประสงค์เพื่อลดการใช้พลังงานต่อปริมาณซอสถั่วเหลืองที่ผลิตได้ 1 ลิตร ซึ่งผลนั้นเป็นที่น่าชื่นชมและการใช้พลังงานก็ลดลงอย่างมาก
Paul Meerman อธิบายว่า “ถึงแม้ตลาดของ Kikkoman จะมีซอสถั่วเหลืองหลากหลายแบบ แต่พื้นฐานของซอสนั้นเหมือนกัน และไม่ใช่แค่พื้นฐานที่เหมือนกันเท่านั้น แต่วิธีการผลิตก็เหมือนกันในทุกแหล่งทั่วโลก ในทางทฤษฎีแล้ว จะต้องไม่มีความแตกต่างกันระหว่างซอสถั่วเหลืองที่ผลิตจากเนเธอร์แลนด์และที่ผลิตจากแหล่งอื่นๆ ทั่วโลก โดยรสชาตินั้นจะต้องเหมือนกันทั่วโลก และผลิตภัณฑ์ที่ได้พัฒนามาใหม่ล่าสุดคือซอสถั่วเหลืองที่ปราศจากกลูเต็น”
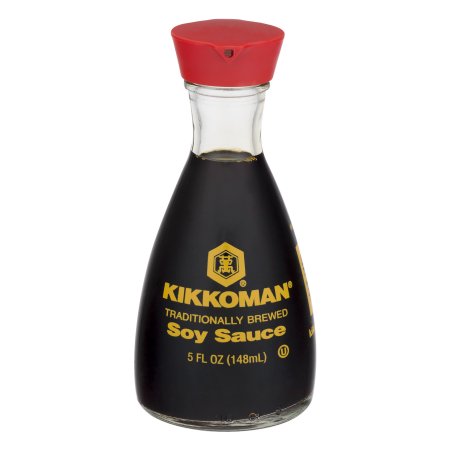
อากาศอัดเป็นส่วนที่มีความสำคัญของการผลิต
นอกจากไฟฟ้า ก๊าซ และน้ำ ทาง Kikkoman ก็มีการใช้พลังงานไปกับอากาศอัดด้วย โดยอากาศอัดเป็นส่วนที่มีความสำคัญในกระบวนการผลิตและเป็นส่วนที่ใช้ต้นทุนสูง เป็นเวลาซักพักแล้วที่ทาง Kikkoman ได้ทำการศึกษาทางเลือกเพื่อการลดการใช้พลังงานในระบบอากาศอัด ซึ่งเป็นส่วนหนึ่งของโปรแกรมการลดต้นทุนการผลิตของซอสถั่วเหลือง
VPVision และ VPFlowScope flow meters สำหรับการวัดแบบต่อเนื่อง
เพื่อที่จะตรวจวัดปริมาณการใช้อากาศอัดของทั้งโรงงาน ทาง VPInstruments ได้ติดตั้งเซ็นเซอร์วัดอัตราการไหลของอากาศอัด (Compressed air flow meter) กับท่อขนาด 25 ถึง 76 มิลลิเมตร (1 ถึง 3 นิ้ว) ในแต่ละแผนก โดย Pascal van Putten (CEO ของ VPInstruments) อธิบายว่า “เซ็นเซอร์วัดอัตราการไหลของอากาศอัดทั้งหมดนี้ได้ทำการอ่านค่าอย่างต่อเนื่อง และส่งข้อมูลการวัดเข้าระบบแสดงค่า VPVision ที่ติดตั้งในห้องคอมเพรสเซอร์ หน้าจอจะแสดงผลการใช้อากาศอัดของแต่ละแผนกในโรงงาน แบบเรียลไทม์ และยังมีการแสดงค่าเป็นแบบกราฟวงกลม (Pie charts) เพื่อดูว่าจุดไหนที่ใช้อากาศอัดปริมาณมาก”
Renting เสริมว่า “แผนกซ่อมบำรุงได้สำรวจว่ามีการรั่วของอากาศอัด (compressed air leaks) หรือไม่ในช่วงที่ระบบมีการใช้ลมน้อย (off-peak hours) โดยทางแผนกจะมีการตัดสินใจว่าจะทำการแก้ไขทันทีหรือสามารถเลื่อนการซ่อมออกไปได้ ขึ้นอยู่กับความรุนแรงของการรั่วที่พบ เพราะบางครั้งก็ไม่สามารถทำการแก้ไขรอยรั่วได้ทันทีที่พบ เนื่องจากยังมีกระบวนการผลิตที่ยังมีความจำเป็นที่ต้องใช้งานอากาศอัดอยู่ในขณะนั้น”
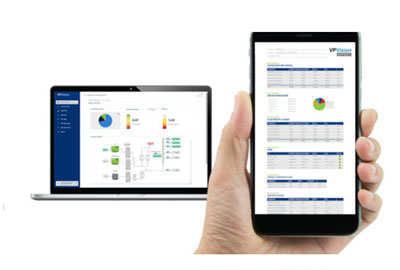
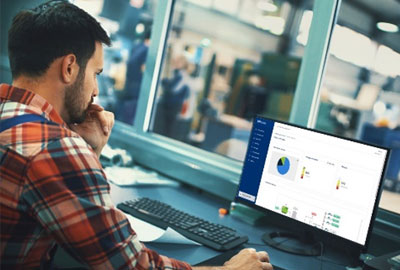
ลดการใช้อากาศอัดได้ถึง 32%
Meerman เสริมว่า “ตั้งแต่เราเปิดโรงงานนี้ในปี 1997 เราประสบความสำเร็จในการลดการใช้พลังงานจากอากาศอัดเพียงอย่างเดียวถึง 32%! ตอนนี้พวกเรามีเครื่องวัดอัตราการไหลของอากาศอัดใช้อยู่ 6 ตัว และกำลังจะเพิ่มเป็น 8 ตัว ติดตั้งให้ครบทุกแผนก เพื่อที่จะมีการตรวจวัดกระบวนการผลิตให้ได้ผลดี จึงเป็นเรื่องสำคัญที่เราจะสามารถแยกค่าการตรวจวัดสำหรับแต่ละแผนกได้ ซึ่งในตอนเริ่มต้นเราไม่สามารถทำได้ ณ ตอนนั้น เราใช้ท่อเมน 1 ท่อกับท่อย่อยหลายๆ ท่อสำหรับแต่ละแผนก ซึ่งทำให้การตรวจวัดมีความยุ่งยาก”
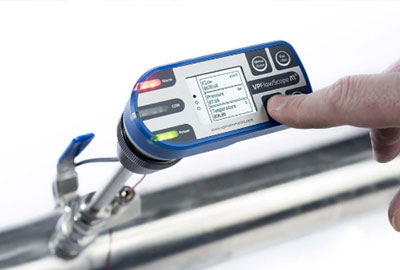
ตอนนี้เรามี distribution station ที่จะแยกอากาศอัดไปฝั่ง supply ให้เหมาะสม ถ้าจะมีการซ่อมบำรุงในแผนกที่ต้องการ ก็จะมีการปิดการใช้งานอากาศอัดในส่วนนั้นชั่วคราว นอกจากนี้เรายังสามารถวิเคราะห์ทางเลือกที่จะปิดการใช้งานอากาศอัดชั่วคราวในบางแผนกที่ไม่มีการใช้งานได้ เพื่อช่วยลดการใช้อากาศอัดได้มากขึ้นอีก
โรงงานของคุณควรที่จะได้รับการตรวจวัดการใช้พลังงานแบบเรียลไทม์
โรงงาน Kikkoman ทั่วโลกจะมีการเปรียบเทียบการประหยัดพลังงานทุกปี เพื่อลดปริมาณการใช้พลังงานต่อซอสถั่วเหลืองที่ผลิตได้ 1 ลิตร ซึ่งโรงงานที่เนเธอร์แลนด์ก็มีคะแนนดีเนื่องจากส่วนของการผลิต โดย Renting ได้กล่าวว่า “เรายังมุ่งมั่นที่จะรักษาระดับนี้ให้ได้ในอนาคต และเรายังคงมีการตรวจสอบระบบใหม่ทุกระบบที่ได้มีการติดตั้งอย่างละเอียดเพื่อดูระดับการใช้พลังงานของระบบ”
สนใจผลิตภัณฑ์ติดต่อ คุณปทิตตา โทร : 088-924-9644 / 092-258-1144 หรือ Lined ID : @entech